Table Of Contents:
- Key Takeaways
- Understand the Importance of Proper Packaging for Acoustic Panels
- Choose the Right Packaging Materials for Acoustic Panels
- Follow Steps to Safely Pack Your Acoustic Panels
- Comply With Shipping Regulations for Acoustic Panels
- Find a Reliable Shipping Service for Acoustic Panels
- Learn Tips to Reduce Shipping Costs for Acoustic Panels
- Conclusion
Are you struggling with shipping acoustic panels safely and cost-effectively? This guide will provide essential insights into proper packaging techniques, choosing suitable materials, and navigating shipping regulations. We’ll explore how to select reliable shipping services and offer tips to reduce logistics costs. By the end, you’ll have the tools and knowledge to ensure your acoustic panels arrive at their destination undamaged, saving you time and money.
Key Takeaways
- Proper packaging is crucial for protecting acoustic panels during shipping and maintaining their integrity
- Sturdy boxes and protective padding are essential for safeguarding acoustic panels from damage in transit
- Clear labeling and compliance with carrier guidelines ensure efficient delivery and proper handling of panels
- Comparing shipping options and tracking shipments helps optimize costs and ensure timely delivery of acoustic panels
- Bulk shipping and rate negotiation can significantly reduce costs for acoustic panel manufacturers and distributors
Understand the Importance of Proper Packaging for Acoustic Panels
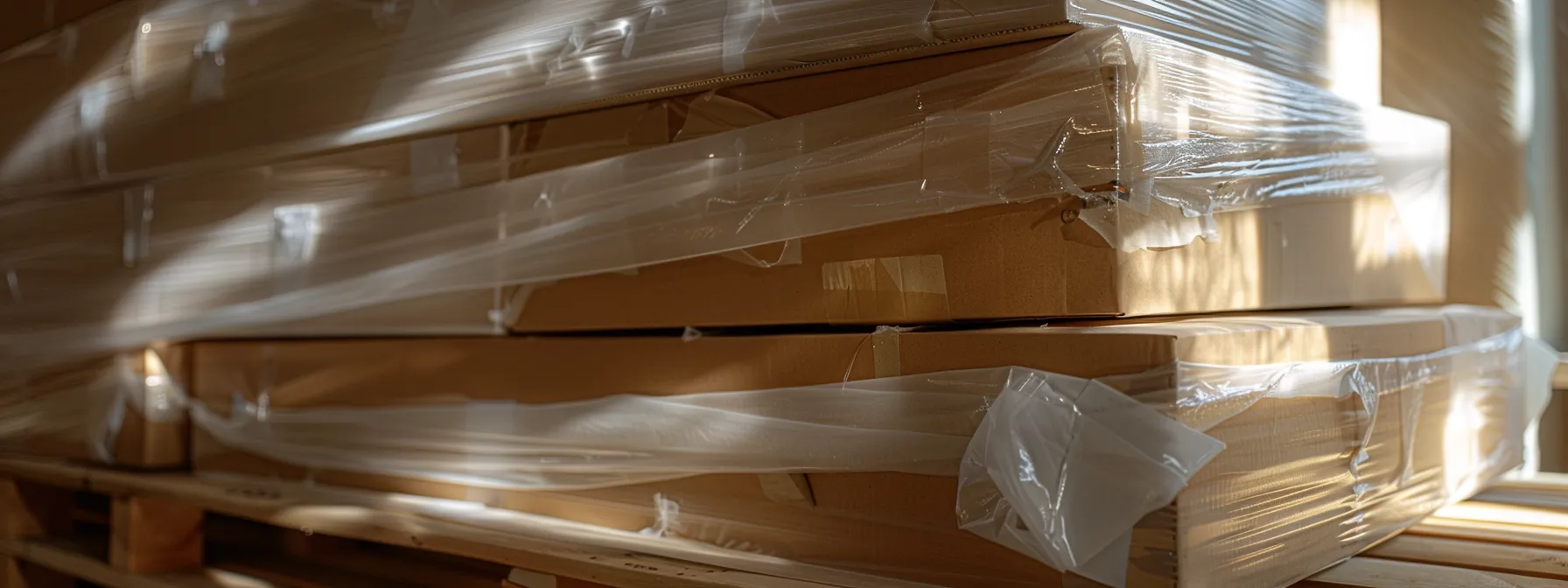
Proper packaging is crucial for acoustic panels, including slat panels, to ensure their safe arrival and maintain their integrity for room acoustics and interior design. This section explores the fragility of acoustic panels and how effective packaging protects them during transit. Understanding these aspects is essential for preserving the quality of solutions, from panels to pipes, throughout the shipping process.
Recognize the Fragility of Acoustic Panels
Acoustic panels are delicate structures that absorb sound waves and improve room acoustics. Their effectiveness relies on the precise arrangement of materials like moss or wool within a gallery-constructed frame. The fragile nature of these components makes acoustic panels susceptible to damage during transit, potentially compromising their performance in the intended space.
The dimensions and shape of acoustic panels contribute to their vulnerability. More extended panels or those with unique designs, such as slat panels, require extra care in packaging to prevent bending or warping. Even minor damage to the panel’s surface or internal structure can significantly impact its sound-absorbing properties, rendering it less effective in controlling room acoustics.
Understanding the fragility of acoustic panels is crucial for manufacturers, installers, and end-users alike. Proper handling and packaging techniques must be employed to protect these sensitive products throughout shipping. This ensures that when the panels arrive at their destination, they are in optimal condition to enhance the acoustic environment of the space.
Learn How Packaging Protects During Transit
Adequate packaging protects acoustic panels during transit from potential damage. For acoustic slat panels, which often feature delicate wooden elements, custom-fitted plastic wrapping provides a barrier against moisture and physical impacts. This protection is especially crucial when shipping panels to home theater rooms, where pristine conditions are essential for optimal performance.
Multi-layered packaging solutions offer comprehensive protection for acoustic panels. Foam inserts and corrugated cardboard layers absorb shocks and vibrations, preventing damage to the panel’s core materials, such as polyester fibers. This multifaceted approach ensures that even when panels are transported to challenging gallery environments, like concrete structures, they arrive intact and ready for installation.
Strategic packaging design also considers unique shapes and sizes. Reinforced corners and edge protectors prevent bending or warping during handling and transportation. For larger panels or custom installations, modular packaging systems allow for secure stacking and efficient use of space, reducing the risk of damage while optimizing shipping costs.
With the importance of packaging clear, it’s time to select suitable materials. The choice of packaging can make or break your acoustic panels’ journey.
Choose the Right Packaging Materials for Acoustic Panels
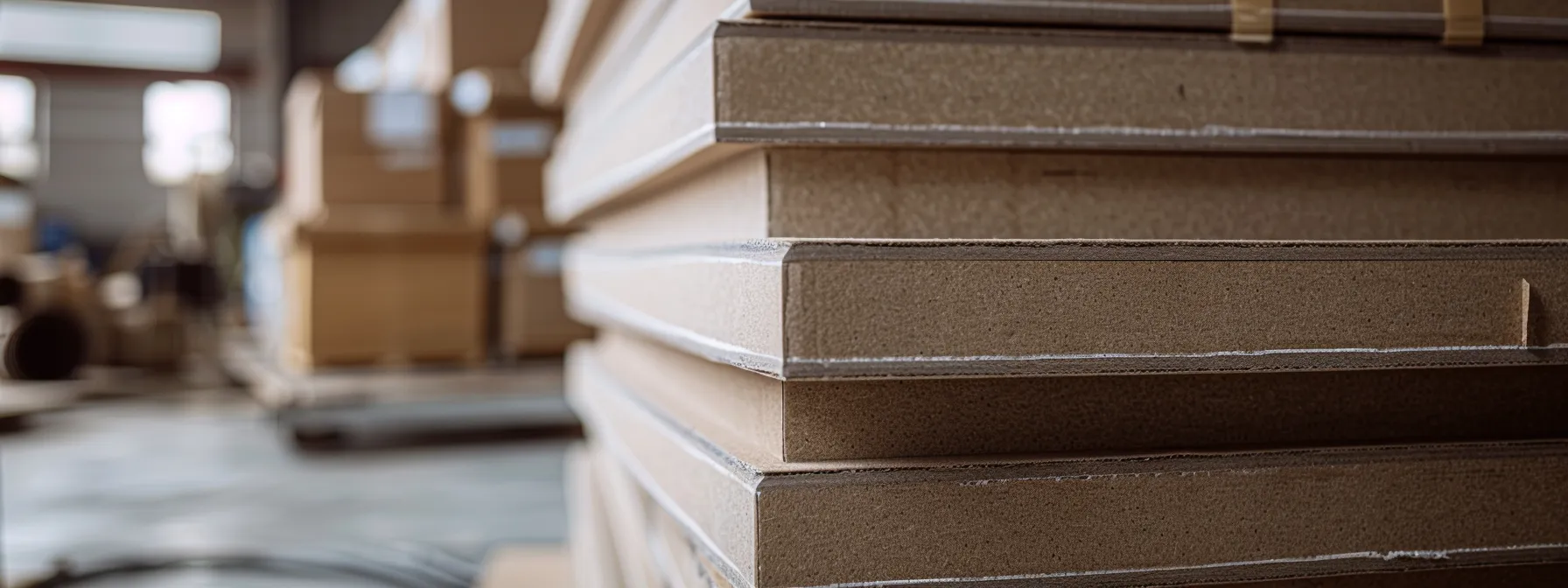
Selecting appropriate packaging materials is crucial for protecting acoustic panels during shipping. This section covers the importance of sturdy boxes and protective padding to ensure panels arrive undamaged. Proper packaging safeguards the panels’ thermal insulation and noise reduction properties and reflects excellent customer service. The following topics explore critical considerations for acoustic panel packaging.
Select Sturdy Boxes Suitable for Acoustic Panels
Selecting sturdy boxes for acoustic panels ensures their safe transport and quality. The boxes should be made of high-quality corrugated cardboard that can withstand the weight and dimensions of custom acoustic panels. This ensures proper protection during shipping, allowing customers to view their purchased gallery panels in perfect condition upon arrival.
When choosing boxes, consider the requirements of glass wool and other delicate materials used in Open Space Dividers panels. Double-walled or triple-walled boxes provide extra strength and protection, especially for larger or heavier panels. These robust containers help maintain the panels’ integrity, ensuring complete coverage of sound absorption capabilities.
Box sizes should be carefully selected to match the dimensions of the acoustic panels, minimizing movement during transit. Custom-sized boxes may be necessary for uniquely shaped or oversized panels. This attention to detail in packaging protects the product and reflects positively on the company’s quality, potentially influencing future payment and repeat business from satisfied customers.
- Choose high-quality corrugated cardboard boxes
- Consider double-walled or triple-walled options for extra protection
- Select box sizes that match panel dimensions to minimize movement
- Use custom-sized boxes for uniquely shaped or oversized panels
Use Protective Padding to Prevent Damage
Protective padding is essential for safeguarding acoustic panels during shipping, especially those with metal components or high-density materials. Foam inserts, bubble wrap and air pillows provide cushioning that absorbs shocks and vibrations, preventing damage to the panels’ delicate structures. These materials help maintain the integrity of the panels, ensuring they arrive at their destination ready for installation.
Custom-cut foam inserts are particularly effective for protecting panels with unique shapes or protruding elements. These inserts cradle the panels securely, minimizing movement and reducing the risk of damage during transit. For panels with wire mesh or other sensitive surfaces, using soft, non-abrasive materials like microfiber cloth as an additional layer of protection can prevent scratches or other surface imperfections.
When packaging acoustic panels, it’s crucial to consider the Application time and handling requirements. Proper padding protects the panels and streamlines the unpacking process for customers. Clear labeling and easy-to-remove protective layers can significantly reduce installation time and improve customer satisfaction. Customers should contact the manufacturer directly for any questions or special packaging requests.
Selecting suitable materials is crucial, but it’s only half the battle. Now, let’s explore the step-by-step process of packing your acoustic panels safely and efficiently.
Follow Steps to Safely Pack Your Acoustic Panels
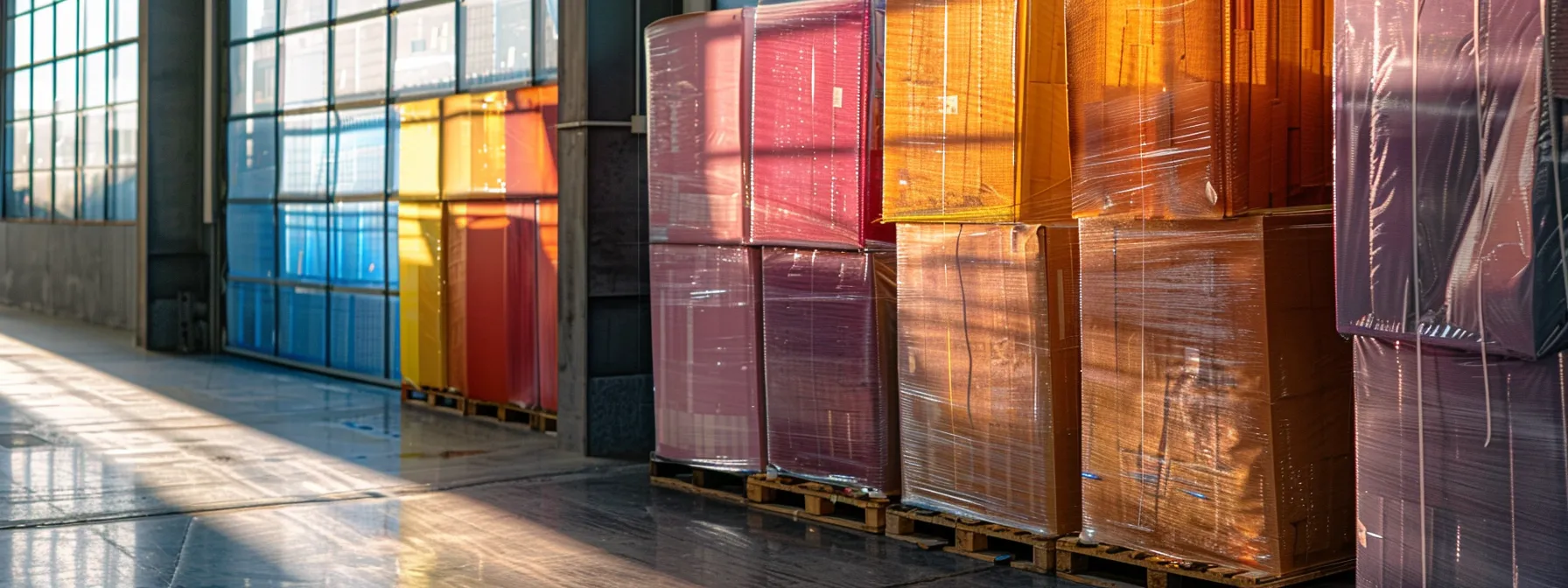
Properly packing acoustic panels is crucial for safe shipping and maintaining their quality. This section outlines essential steps for wrapping individual panels with protective material and securing them within boxes to minimize movement. These techniques ensure that panels, including those for home theaters and furniture, arrive undamaged, preserving the brand’s reputation and customer satisfaction.
Wrap Each Panel Individually With Protective Material
Individually wrapping acoustic panels with protective material ensures suitable materials is crucial, but it’s only half the battle. Now, let’s explore their safe transport. Each panel should be covered with soft, non-abrasive materials to protect against scratches and dust. This solution safeguards the panel’s surface and helps maintain its structural integrity during shipping.
When selecting wrapping materials, it’s essential to consider the panel’s composition, including any cellulose or formaldehyde-free components. Acoustic panels or microfiber cloths are excellent choices for the initial layer, as they won’t react with the panel’s materials. This careful selection process helps preserve the panel’s acoustic properties and appearance.
After the initial wrapping, panels should be encased in bubble wrap or foam sheeting. This additional protection is essential for panels with specialty lumber or delicate surface textures. This method ensures that the panels arrive at their destination in pristine condition and ready for installation by providing comprehensive coverage.
Secure Panels Within the Box to Minimize Movement
Securing acoustic panels within the box minimizes movement during shipping, ensuring customers receive undamaged products for soundproofing needs. Use foam corner protectors and insert rigid cardboard dividers between panels to prevent shifting. This method is particularly effective for slat wood panels, which require extra care to maintain their aesthetic appeal and properties.
For larger shipments, consider using custom-fit foam inserts or air pillows to fill void spaces within the box. This approach protects melamine-faced panels and enhances the package’s overall stability. Proper securing techniques are essential for preserving the integrity of soundproofing solutions designed for music rooms or recording studios.
When packing multiple panels, alternate their orientation to distribute weight evenly and reduce pressure points. This strategy is especially beneficial for delicates in professional settings. The following table outlines effective securing methods for different types of panels:
Packing complete, the panels sat ready. Now, shipping laws demanded attention.
Comply With Shipping Regulations for Acoustic Panels
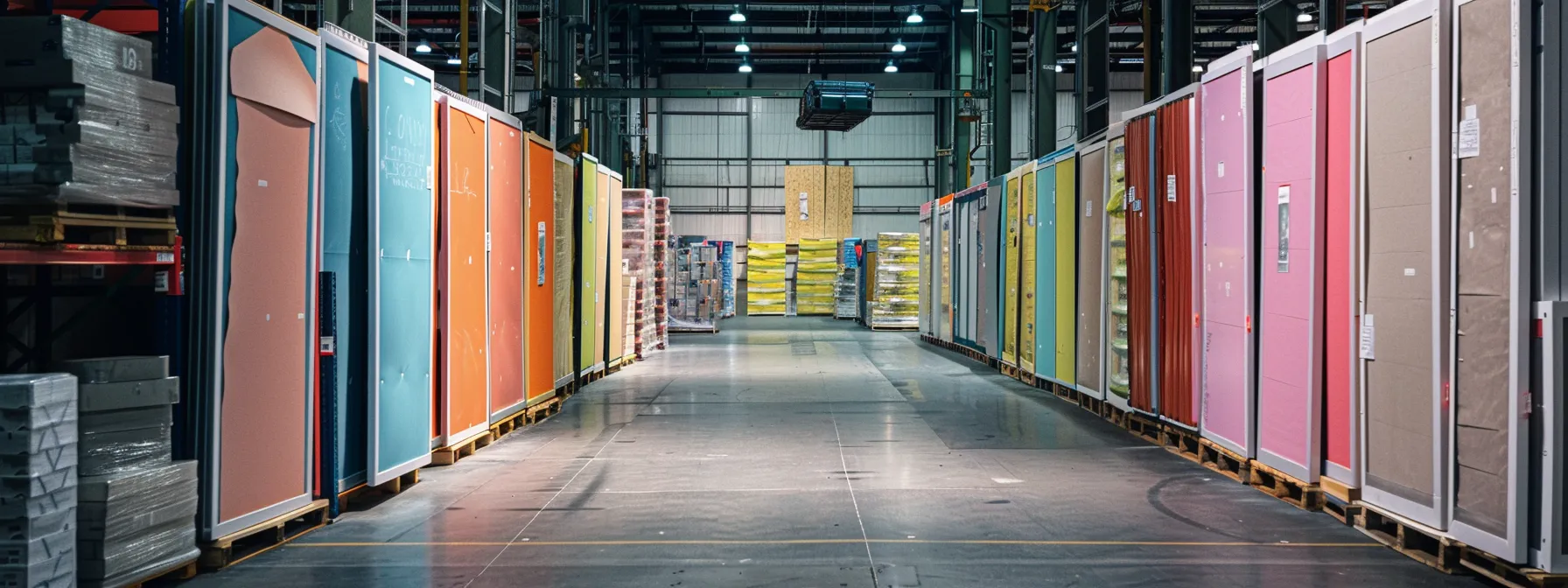
Complying with shipping regulations is crucial when transporting acoustic slat panels and other noise-reduction products like Owens Corning. This section examines carrier guidelines for shipping, including considerations for color options and materials like moss-moss. It also covers the importance of clear package labeling to ensure efficient cargo delivery and maintain product integrity throughout transit.
Check Carrier Guidelines for Acoustic Panel Shipping
Checking carrier guidelines is essential when shipping acoustic panels as building materials. Carriers often have specific requirements for packaging and transporting delicate items like acoustic products.
Carriers may have restrictions on panel sizes, weight limits, and packaging materials. Understanding these limitations enables shippers to prepare acoustic panel applications properly for transit. Some carriers might require additional protection or special handling for acoustics products, which could impact shipping costs and delivery times.
Compliance with carrier guidelines ensures smooth transportation and reduces the risk of damage or delays. Shippers should consider the following factors when preparing acoustic panels for shipment:
- Panel dimensions and weight
- Packaging materials and methods
- Special handling requirements
- Insurance options for valuable acoustics products
- Delivery timeframes and tracking capabilities
Label Packages Clearly for Efficient Delivery
Clear labeling of packages containing acoustic sound panels is crucial for efficient delivery and proper handling. Shippers should prominently display “Fragile” and “Handle with Care” labels to alert carriers to the delicate nature of the contents. These labels help ensure the panels’ sound barrier properties and aesthetics remain intact during transit.
Including specific handling instructions on the package can further protect the acoustic panels’ image and absorption capabilities. Labels should indicate the correct orientation for storage and transport, such as “This Side Up” or “Do Not Stack,” to prevent damage to the panels’ delicate surfaces. This attention to detail in labeling helps maintain the panels’ performance and appearance upon arrival.
Accurate and visible recipient information is essential for the timely delivery of acoustic panel shipments. Shippers should print the delivery address, contact details, and any special delivery instructions on the package. This practice minimizes the risk of misrouting and ensures that the acoustic panels reach their intended destination efficiently, preserving their sound-absorbing qualities for immediate installation.
After handling the regulations, the task shifts to finding a trustworthy shipper. The exemplary service ensures your acoustic panels arrive safely, ready to transform spaces.
Find a Reliable Shipping Service for Acoustic Panels
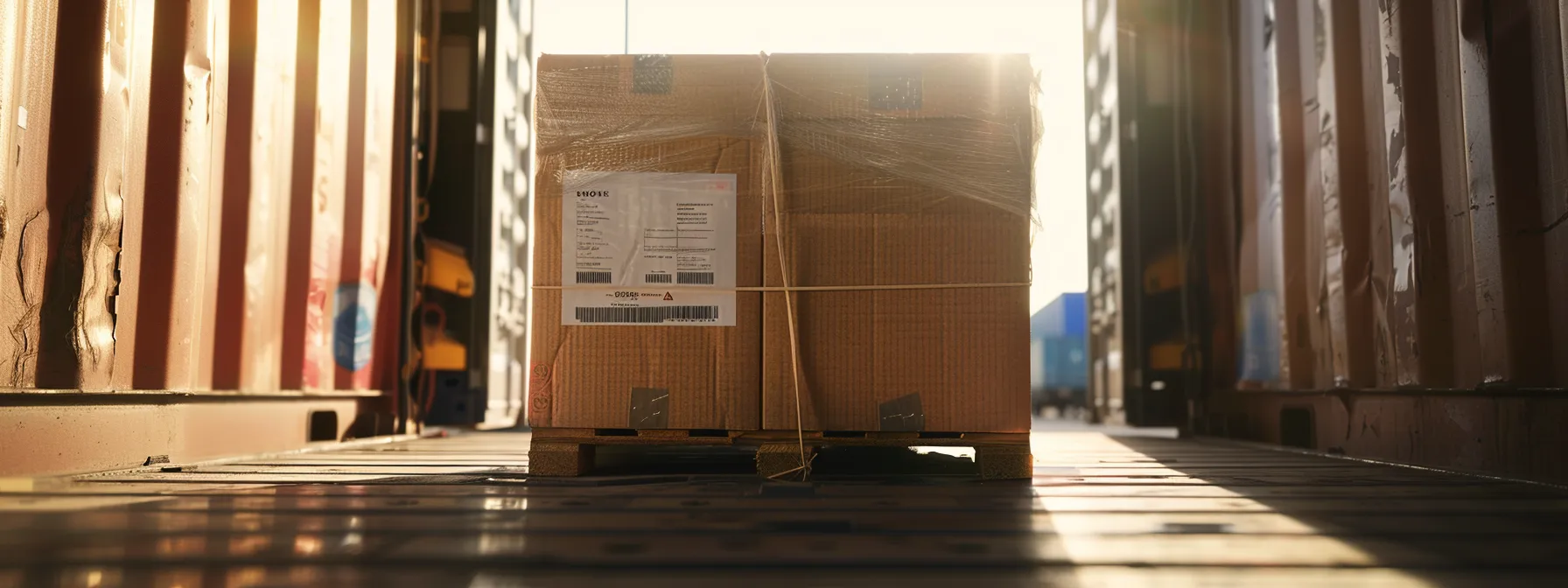
Finding a reliable shipping service is crucial for safely transporting acoustic panels, including wood and hexagon wall panels. This section compares shipping options to identify the best service rates and discusses tracking shipments to ensure timely delivery. These considerations help maintain item integrity and customer satisfaction when shipping acoustic solutions.
Compare Shipping Options for Best Service Rates
Comparing shipping options is crucial for finding the best service rates when transporting acoustic panels. Providers offer services tailored to different needs, from standard ground shipping to expedited air freight. Businesses should evaluate these options based on delivery speed, cost-effectiveness, and care required for delicate acoustic materials like panels and room acoustics solutions.
When assessing shipping services, companies must consider the unique requirements of acoustic panels. Some carriers specialize in handling fragile items and may offer custom crating or packaging services, which can be beneficial for preserving the integrity of painted acoustic panels during transit. Balancing these specialized services with the overall cost is essential to ensure the most efficient and economical shipping solution.
To make an informed decision, businesses should request quotes from multiple shipping providers and compare their offerings. The following table outlines key factors to consider when evaluating shipping options for acoustic panels:
Track Shipments to Ensure Timely Delivery
Tracking shipments of acoustic panels, including room kits and fiberglass products, is crucial for ensuring timely delivery and customer satisfaction. Reliable shipping services offer real-time tracking capabilities, allowing manufacturers and customers to monitor the progress of their acoustic panel shipments throughout the transit process. This visibility enables proactive management of potential delays and provides peace of mind to clients awaiting their acoustic solutions.
Effective tracking systems can provide valuable feedback on the shipping process, helping manufacturers optimize their packaging and logistics strategies. By analyzing delivery times and handling procedures across different carriers, companies can identify the most efficient shipping methods for their acoustic panels, taking into account factors such as panel dimensions and materials used. This data-driven approach can improve shipping outcomes and reduce transit times for future orders.
Accurate tracking becomes even more critical for custom acoustic panel projects with specific installation timelines. Manufacturing facilities can use tracking information to coordinate production schedules with expected delivery dates, ensuring panels arrive on-site when needed. This level of coordination is significant for large-scale acoustic installations or time-sensitive projects where delays could impact overall construction or renovation timelines.
Shipping costs can make or break a project. Here’s how to keep more money in your pocket.
Learn Tips to Reduce Shipping Costs for Acoustic Panels
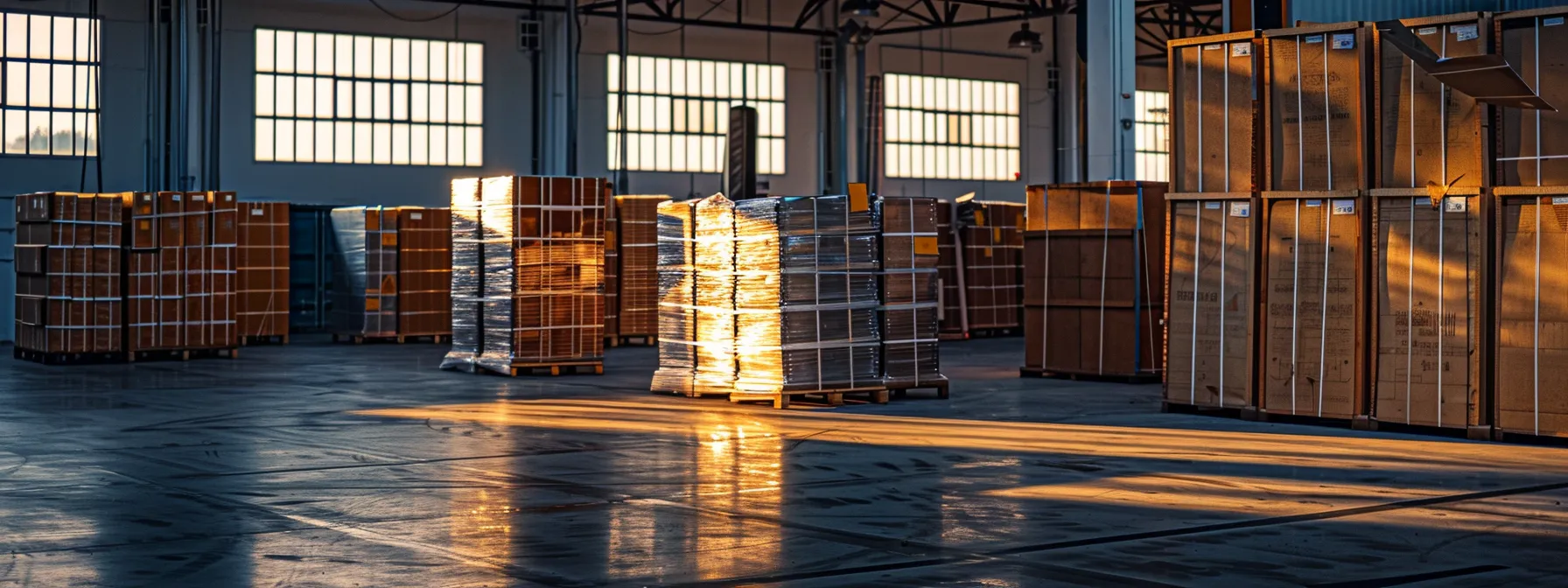
Reducing shipping costs for acoustic panels, including environmentally friendly options and Guilford of Maine products, is crucial for maintaining a competitive edge. This section explores strategies to optimize expenses while ensuring quality delivery. Topics include leveraging bulk shipping for cost savings and negotiating rates with providers to achieve budget-friendly solutions for various acoustic designs, from tiles to custom installations.
Opt for Bulk Shipping to Save on Costs
Bulk shipping offers significant cost savings for acoustic panel manufacturers and distributors. By consolidating multiple orders into one shipment, companies can reduce per-unit shipping costs, especially for items like acoustic foam and adhesives. This approach is efficient when supplying large projects or recurring customers, allowing businesses to pass on savings to clients while maintaining profitability.
When opting for bulk shipping, careful planning is essential to maximize efficiency. Manufacturers should consider factors such as the dimensions of acoustic panels, which are often measured in square feet, and the weight of materials like screws and mounting hardware. Companies can minimize wasted space and reduce shipping costs by optimizing packaging and pallet configurations.
Bulk shipping can help streamline customs processes and reduce associated fees for international shipments. By consolidating shipments, businesses can minimize paperwork and potentially qualify for preferential rates or expedited clearance. This strategy not only saves money but also reduces the likelihood of delays at customs, ensuring timely delivery of acoustic panels to international clients:
Negotiate Rates With Shipping Providers
Negotiating rates with shipping providers can significantly reduce costs for acoustic panel manufacturers, especially when shipping textile-covered panels or wood veneer products. Companies should leverage their shipping volume data to demonstrate their value as customers and negotiate more favorable rates. This approach can yield substantial savings, particularly for businesses that frequently ship large acoustic panels.
When negotiating, manufacturers should consider the unique characteristics of acoustic panels, such as their dimensions and weight, which may affect shipping costs. By discussing these specifics with providers, companies can secure rates that accurately reflect the nature of their products, potentially avoiding oversized or overweight charges. This tailored approach can result in more cost-effective shipping solutions for items customers frequently add to their carts.
Manufacturers should also explore multi-carrier strategies to optimize shipping costs. By comparing rates from different providers for various routes and panel types, including those designed for drywall installation, companies can select the most cost-effective option for each shipment. This flexible approach allows businesses to adapt to changing market conditions and maintain competitive pricing for acoustic panel solutions.
Conclusion
Proper packaging and shipping of acoustic panels are crucial for preserving their integrity and performance. Understanding the fragility of these products, selecting appropriate packaging materials, and following precise packing steps ensure safe transit and customer satisfaction. Adhering to shipping regulations, choosing reliable carriers, and implementing cost-effective strategies like bulk shipping and rate negotiation are essential for efficient and economical delivery. By prioritizing these aspects, manufacturers and distributors can maintain product quality, reduce costs, and enhance their reputation in the competitive acoustic solutions market.